In this guest article, Luigi Monaco, an entrepreneur from Aschaffenburg with a focus on 3D printing in plastic, presents an innovative project: the development of the “ocanom GT Racer” saddle for his Triumph Speed Twin. This article sheds light on how Monaco addresses a problem of seat ergonomics in café racers through individual adjustments and the use of 3D printing technologies and creates a tailor-made solution that combines comfort and design.
My private project commenced in the summer of 2021, when an extended journey on my Triumph Speed Twin to a friend’s abode presented unforeseen challenges—pain compelled me to conquer the final 100 kilometers standing. Despite attempts to mitigate discomfort through additional padding, the issue persisted. The quest to identify the cause yielded no definitive results, yet it became evident that the seat’s ergonomics were suboptimal. The seats of Café Racers are often narrow, which, while beneficial to the design, compromises comfort. Given the aftermarket’s lack of suitable solutions, I found myself compelled to devise a solution independently.
To circumvent the issues with pressure distribution due to the narrow saddle during test rides aimed at finding the optimal seating position, I opted for a wider-shaped seat from the chopper segment, offering a 3-point mounting system. To allow for flexible adjustments in seat height and tilt angle, I devised a special bracket for the saddle, which was based on a Tamarit Suzuka rear tail fairing and facilitated adjustments along the X- and Y-axis.

Armed with insights gained from test rides about the optimal saddle position and inclination, I was able to establish a solid foundation for the final design. Particularly illuminating was the discovery that the seat’s recess functions ideally during acceleration, yet the front, narrowly tapering part offers no support during braking, causing discomfort. These valuable insights culminated in the creation of a new scan of the motorcycle, including the tank and tail fairing, which served as the basis for the final design development.
In the subsequent step, the sketching of the basic lines commenced in Autodesk Inventor, which were then shaped into a solid. The design of the areas where the tank contacts the saddle and where the tail fairing connects to the saddle was based on the scan, converted into surfaces in Rhino and with Mesh2Surface. These contact areas were thickened, transformed into a solid, and ultimately subtracted from the main body via a Boolean operation. The entire design was implemented on a symmetrical half, which was then mirrored and finalized with fillets to perfect the final shape. The dimensions on the spline curves of the elevations allow for iterative optimization after each print and test ride.

The five saddles created to date were printed on a CreateBot D600 Pro2, which I had ordered directly from China in November last year. TPU posed a minor issue, for which I fabricated a small SLS part that forces the filament guidance into axial alignment after the drive, before the extruder. A special thanks to CreateBot at this point for sending me the STEP file of the head, sparing me a great deal of work. A single print takes approximately three days and uses about 2kg of Overture TPU95A black filament.

Of course, besides the shape, the firmness of the seat is crucial. For this purpose, I filled the created geometry in a Prusa Slicer with around 8% gyroid infill, which allows for efficient force absorption in the X, Y, and Z axes as well as air permeability within the saddle, thereby negating the effects of air compression in small volumes. Currently, I am using a wall thickness of 3 lines with the 0.8mm nozzle. Future optimizations may involve dividing the infill strength into zones, possibly with enclosed air chambers, as well as reducing the wall thickness of the outer shell. I can already confirm that this saddle is worlds apart from anything I’ve ridden on the Speed Twin before. Particularly noteworthy is the thermal insulation in cold weather and the damping behavior enabled by the large air chamber, which makes a difference especially on rough roads. Now, the TPU-made saddle faces the challenge of proving its everyday practicality and reliability under various environmental conditions.
I’ve named the saddle “ocanom GT Racer,” ‘ocanom’ because it’s my surname spelled backwards, ‘GT’ for Grand Tour, and ‘Racer’ due to its origin from the Café Racers. I look forward to the upcoming motorcycle season and hope that this article serves as a stimulus and occasion for discussion.
The ‘ocanom GT Racer’ is dedicated in the spirit of the Amazon Grand Tour series, as well as the YouTube channels RACER TV and SuperBike Italia, as a token of gratitude for the joy and inspiration provided during the dark winter months whilst crafting the saddle 😉
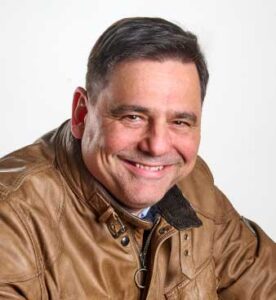
Subscribe to our Newsletter
3DPResso is a weekly newsletter that links to the most exciting global stories from the 3D printing and additive manufacturing industry.